Many of today’s ironmaking facilities could benefit massively from more thorough digitalization of processes.
We sat down with Dieter Bettinger, Product Manager for Ironmaking Automation at Primetals Technologies, to
talk about his perspective on the state of digitalization
in ironmaking today, the potentials offered by artificial intelligence, and the crucial difference between data and information.
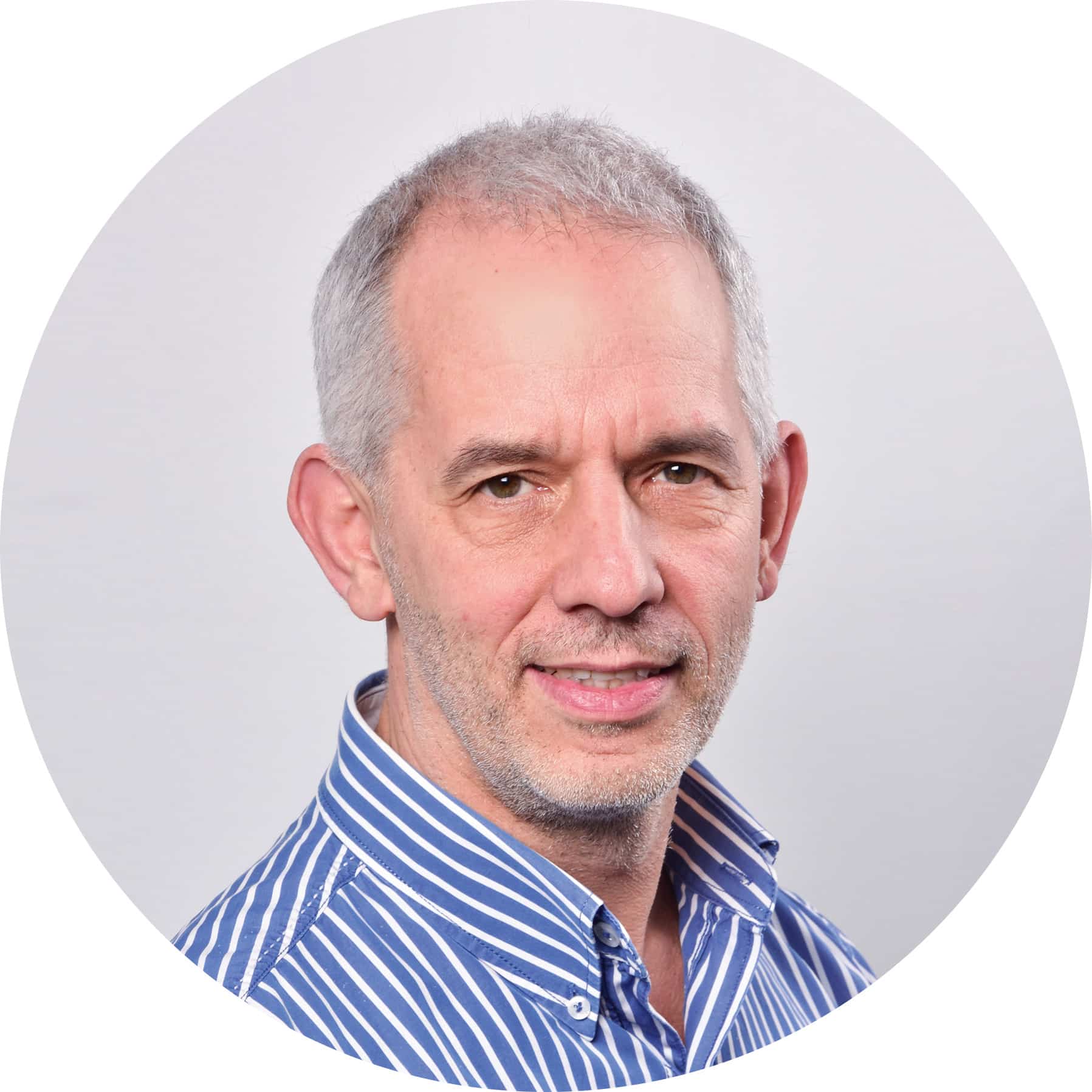
What potential for improvement do you see in ironmaking plants in terms of process optimization systems?
Dieter Bettinger: In many plants, you can still easily identify shift-dependent operation—which is particularly unfavorable for plants with process times in the same range as shift duration. In many cases, it is quite straightforward to calculate the related saving potential.
What was the starting point for the development of ironmaking process optimization?
Bettinger: From the very beginning, the main motivation for developing ironmaking process optimization solutions was to reduce conversion costs—in other words, to save money. The basic approach is to develop a standardized operation philosophy, which is then executed by the automation system. The great success of our approach based on an Expert System is the continuous improvement that can be achieved in the process: If the operator or process engineer finds additional room for improving the operation, he or she can easily add new insight to the system—because of the continuous dialog with it. This increases the knowledge base of the system. It took years of close cooperation with our metallurgical partner voestalpine to reach a level of trust in our technology that allowed them to go for closed-loop operation. But in the end, they saw that a well-maintained Expert System is hard to beat in terms of reliability and cost savings.
There are several new measuring systems available— how do you use the related information?
Bettinger: The paradigm of our approach is first to extract information from data—and then to use this information to provide the basis for actions. Data is not relevant as long as no information is generated; information is useless if not used to trigger actions. For this reason, measurement systems that are not fully integrated into the process optimization system are not used at their full potential. Additionally, many plants only use a small fraction of the history data—wasting an important source for operational improvements.
A huge amount of data is created in modern iron- making plants—how can it be efficiently used?
Bettinger: The important task of data mining is transforming the huge data sets stored in the automation systems into information that is actually valuable. Our automation systems are ready to interface with data mining tools. In addition, we have data scientists—specialists with data preparation knowledge, data analytics skills, and domain know-how—who can provide efficient support services to help the customer get more out of their data.
How do you judge the impact of digitalization?
Bettinger: The merging of classical automation technology with information technology has already started and it offers huge potential. At the same time, connecting local automation to other systems will introduce big challenges to the industry, as it potentially opens doors to hackers and other intruders. It is important to prepare professional security concepts for these challenges.
What is the relevance of artificial intelligence for state-of-the-art process optimization?
Bettinger: There has been a revival of artificial intelligence, most recognizably in applications highly visible to the public, such as autonomous vehicles. Understanding human language, developing faculties in strategic game systems (such as chess and Go), intelligent routing in content delivery networks—these are other applications. There is definitely potential for applications in the iron and steel industries, as long as human intervention is possible to identify impact factors for key performance indicators, to do pattern recognition, to perform data analytics, and to optimize plant operation. However, we are still very selective in incorporating AI solutions directly into control systems, to avoid unforeseen actions.