Metals Magazine speaks with Kaptan’s Yaşar Çebi about his company, its focus areas and goals, and the recent investment in a wire-rod mill upgrade, with which Primetals Technologies was tasked. Kaptan, a family-run enterprise headquartered in the city of Istanbul, Türkiye, is in the process of expanding its product portfolio into the realm of quality steels for demanding industries including the automotive sector—whilst maintaining a strong foothold on the domestic and international market.
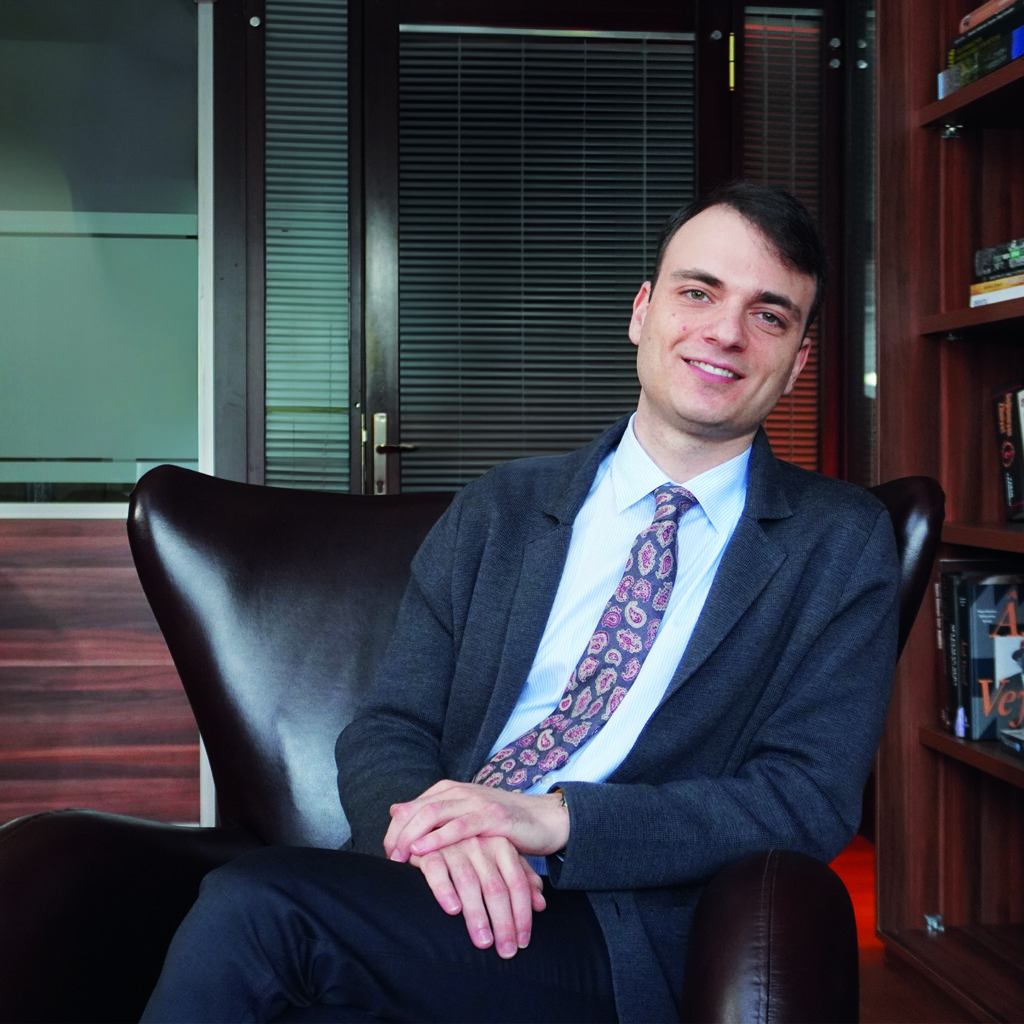
Kaptan Demir Çelik has been a family-run business for over 60 years, with your generation of leaders representing the third. Was it always clear to you that you would choose this path?
Yaşar Çebi: I have long considered it my duty to follow in my grandfather’s and father’s footsteps. I started working at the steel plant at age 18, meeting the workers and spending at least 50 percent of my time on-site. Today, I still profit from that experience because it helps me understand steel production on a real-world, day-to-day level. I now do most of my executive work from the office, but I am no stranger to the “active” tasks performed in the plant.
I am sure you are proud of your company’s legacy …
Çebi: Yes, of course I am proud of the achievements of our company and of my family. In my view, the hardest thing is to go “from zero to one,” effectively making something out of nothing. Building a new business and turning it into a success is a major challenge. Once everything works, the refining of it is somewhat more straightforward. However, as time progresses, the world changes—and this can lead to a situation that forces you to revisit certain decisions you made early on, and to potentially shift into a new direction. When this happens, it is almost as demanding as going from zero to one. I believe that my generation of company leaders will experience and facilitate significant change.
Can you give me one example of this kind of change?
Çebi: On the technology side, one simple example is that of enterprise resource planning software. Nowadays, it is standard to use SAP or a similar solution, whereas for many years Excel files were sufficient. And while there is always reluctance to “change a winning team,” we must sometimes recognize the need to adapt.
We aim to produce high and medium carbon steels using the electric arc furnace route.”
What products are you currently focusing on?
Çebi: Right now, our main focus is on rebar and wire rod for both the Turkish and international markets. Additionally, we are seeing an opportunity in the field of value-added products and will be moving more into that direction. Our aim for the years ahead is to produce high and medium carbon steels using the electric arc furnace route.
Kaptan Demir Çelik is part of the larger Kaptan Group, which was founded in 1964 when Kaptan Steel & Iron Company established its first rolling plant. Being the first and only steel plant in the Thrace region, the facility enjoyed the benefits of excellent accessibity: it was located only three miles from the main highway and some four miles from the Martaş port. These logistical advantages gave Kaptan a competitive edge. Today, Kaptan Group covers areas as diverse as iron and steel, logistics, shipping, energy, recycling, mining, and strategic investment. Steel production continues to be central to Kaptan, and more production facilities have been added over time. The Çorlu rolling plant has a yearly capacity of 650,000 tons of rebar and was started in 1991. In Marmara Ereğlisi, another plant commenced operations in 2002, then capable of producing 1.4 million tons of billets. Marmara Ereğlisi is also home to a steelmaking plant, based on a 125-ton electric arc furnace, and to three rolling mills; the most recent rolling mill was commissioned by Primetals Technologies in 2023.
Producers often worry about finding competent staff who can help them move into new product segments. Is it hard to find skilled operators in Türkiye?
Çebi: We are facing no issues when it comes to hiring experienced staff in Türkiye, thanks to the fact that the steel industry in our country is at a mature level. This solid basis is making it easier for us to shift into the quality-steels market.
Primetals Technologies had the honor of doing a complete overhaul of your wire-rod mill. Are you happy with the new production equipment?
Çebi: I can say that the equipment is so good that it pushed us further into the field of high-quality products. It performs so well that we decided to raise the bar in terms of our expectations and ambitions—and of the type of products we want to focus on going forward. In that sense, it was a catalyst for change.
Primetals Technologies recently finalized a wire-rod mill project executed for Kaptan Demir Çelik at the producer’s Marmara Ereğlisi location. The project entailed the construction of a new mill, which is now expanding Kaptan’s portfolio to include such value-added products as coiled rebar, fine grain rebar, and welding wire for the engineering and automotive industries, both domestically and internationally. The new equipment allows Kaptan to be a global leader in terms of product quality. The startup of the new mill was remarkably quick. It took only 21 days from the start of hot commissioning to the first saleable product. This record-setting implementation has established a new industry standard and was made possible thanks to an experienced project team and the close and effective collaboration between Primetals Technologies and Kaptan Demir Çelik. When Kaptan tasked Primetals Technologies with the project, two of the deciding factors were the equipment’s technological advantages and the after-sale services provided by the Istanbul, Türkiye, company location of Primetals Technologies. The new wire-rod outlet has increased the plant’s production capacity and finishing speeds. The mill can roll up to 105 tons per hour at speeds of up to 110 meters per second. Kaptan is now set to offer quality carbon products ranging from 4.5 to 26 millimeters in diameter and rebar in coil at the expanded range of 6 to 20 millimeters. The final acceptance certificate for Kaptan’s new mill was issued in fall of 2023.
Would you say that it was a well-executed project?
Çebi: The start and the completion phases of the project were near-perfect, and any alignment issues we had in the middle were resolved. I played the role of a mediator when we needed to clarify open topics and to find common ground.
How would you describe the collaboration with Primetals Technologies?
Çebi: It was good. The staff at the Istanbul company location of Primetals Technologies were very helpful and responded quickly to our needs. Much of our new equipment was designed by U.S. engineers, and there is obviously a difference in time zones. But together, we managed to overcome our challenges in communication.
Is there anything that you find particularly remarkable about the new mill?
Çebi: We wanted high-speed equipment. Speed was important to us, and it was astonishing to see the mill live up to our expectations—to see it work in our own plant, reliably, like a clock. It was a very gratifying experience.
The new mill comes with extensive Level 1 and 2 automation. Do you think that digital solutions will play an even greater role in the future?
Çebi: Level 2 matters a great deal because you need to obtain production data from the machines rather than from the operators—for instance, information on speed, quality, output, and maintenance-related aspects. If you have this data, you can improve your operations. To answer your question in a broader sense, I am certain that digital solutions are crucial now and will become even more relevant in the future. They can help human operators to deliver even better results and to be more productive. This is true for steel production as well as for other fields.
Can you share with us some of your long-term goals with your plant?
Çebi: Our ambition is to produce high-quality steels, for example for the automotive industry.
What interests you outside of the world of metals?
Çebi: Above all, I love nature, in which I spend much of my time. I also own a dog and a cat, and I like to play chess and computer games.
Do your hobbies inform your strategic decision making?
Çebi: Not really. When you play chess, you can plan something on the board based on factors that are all well-known. It is easy to develop a strategy under such circumstances. In real life, however, all factors are never fully known. You must remain agile, be realistic, make quick decisions, and move fast. Computer games can teach you to be quick and improve your problem-solving skills.
If you could have one wish fulfilled to everyone’s
benefit, what would it be?
Çebi: Peace and justice for us all.