Who are the great women in the world of steel? In this series, we ask them to step into the limelight. The steel industry may long have been a bit more on the conservative side, but this is changing fast. These days, it is only right that Metals Magazine reflect the global trend toward an even more diverse and powerful workforce in steel production.
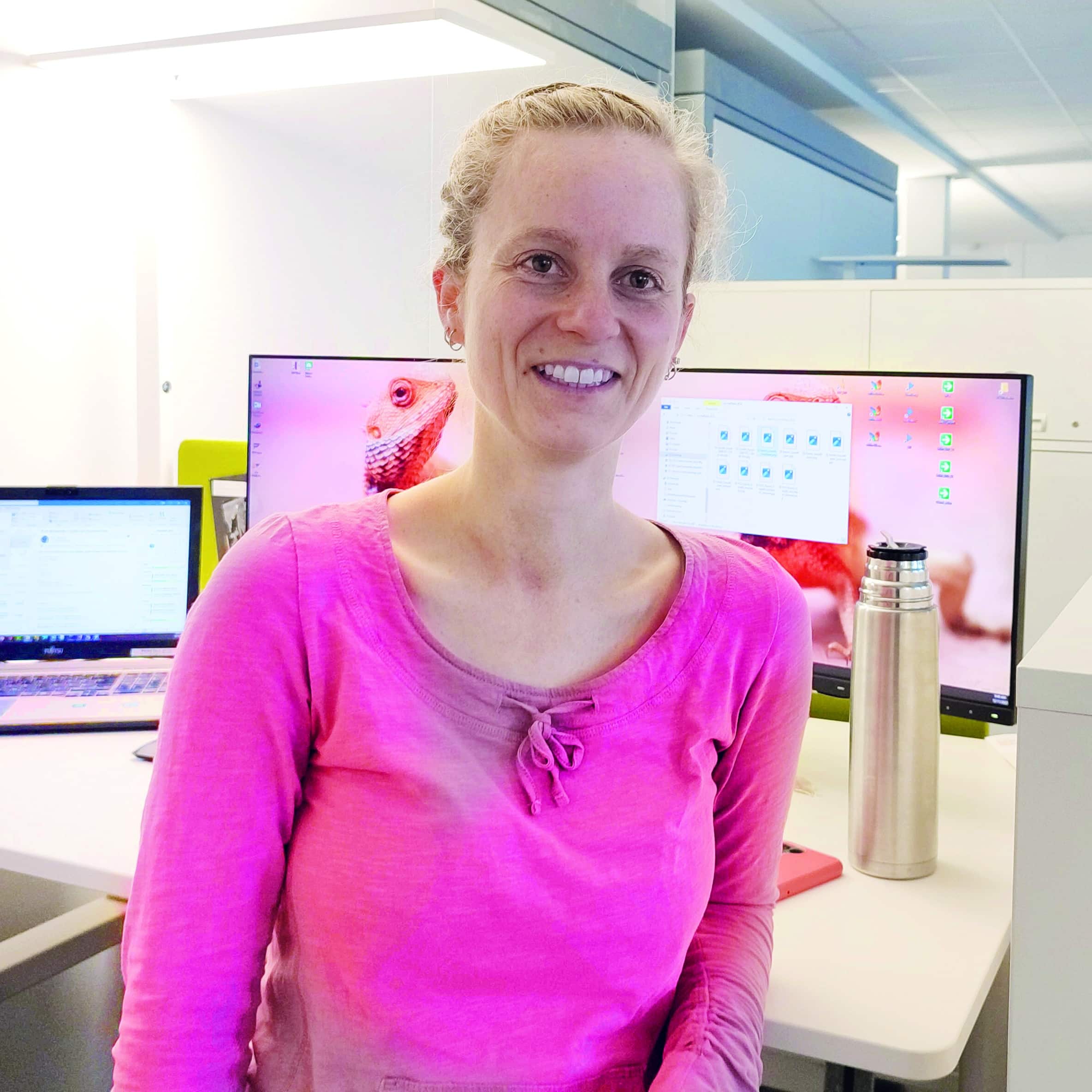
How did you start out in the steel industry?
Karola Gurrath: I studied process engineering at Friedrich Alexander University in Erlangen-Nuremberg, Germany. The program was called “Chemical and Biological Engineering” at the time, and my main interest was in thermodynamics. I then did an internship at Primetals Technologies. It shifted my attention to transformation models, which play a crucial role in steel production. I started to observe and study exactly how steel changes from one state into the next as it cools down.
What was it like to first enter a steel plant?
Gurrath: I was impressed by the sheer size of the rolling mill. It was loud, smelled of oil and grease, and was surrounded by air laden with water vapor. The immediate association I had was that of a spooky castle in a fantasy novel, where the fire-spitting dragon is lurking in the shadows and might just jump at you any second. Even though I never actually spotted the dragon, that first time was hugely memorable. These days, I still enjoy experiencing the process we design hands-on. After all the quiet “lab time,” it is great to see your code running on the real equipment and to feel the immediacy of the process you’ve designed driving the large mill.
What is it about the rolling mill that fascinates you?
Gurrath: We are working with gigantic sizes: the mill is a large beast, and the strip gets longer and longer as it is rolled and becomes thinner. The strip can reach speeds of 15 meters per second … it literally flies through the mill. The challenge for the mill—and the software that runs it—is to ensure near-perfect strip shape in spite of these speeds. And we are meeting this challenge, down to tolerances of a few microns. But to achieve such results, all parameters must be set correctly as the head end of the strip first enters the mill.
In a nutshell, is this what you do—develop the code that controls the mill?
Gurrath: It takes a lot of code for a hot-rolling mill to operate smoothly. My role is tailored to addressing the contour and flatness of the strip. What I program is part of our company’s Level 2 system and ensures that the mill consistently delivers the desired product. After rolling, the strip must be at its target profile, which is usually in the range between 30 and 150 microns. A new development that I implemented, tested, and deployed at the hot-strip mill of a German steel producer was a “box-profile strategy” that allows for target profiles close to zero without destabilizing the strip run.
It’s a great experience to see your code run on the steel-production equipment and to feel the sensation of the process you’ve designed driving the large mill.”
How do you go about executing your projects?
Gurrath: My projects often feel a bit like an “escape room” type of situation to me, where I have to solve problems without a clear or predefined path forward. The steel producer, our customer, may present us with new requirements for its production process, and I then have to find the right solution. There are many things to consider, from the reduction levels to the bending forces. I usually conduct a thorough process analysis to learn where in the code the respective changes must be made. Our code base is very comprehensive. I use a test-driven development approach, which relies on a simulation environment that we developed. This enables us to test every single detail.
You seem to be the kind of person who takes a systematic approach to tackling their challenges …
Gurrath: That is true. I love order and structure, and programming software is very gratifying to me.
What do the final steps look like?
Gurrath: I think that, in software development, you have to remain agile because code is an evolving thing. This characterizes my work and makes it cyclical in nature. However, there are defined deliverables, and once the code is stable and thoroughly tested, I log in to our partner’s servers and upload the new software to their equipment. What happens then is almost like a software update on your smartphone. Once the update is applied and the production process resumes, I check the log files to see if everything is working as intended.
Could artificial intelligence ever do your job for you?
Gurrath: We have been employing artificial neural networks for decades to describe those material properties that still can’t be represented with sufficient accuracy using principal models. Today, I feel that AI—especially in the form of deep learning—carries a lot of potential to enrich my work. We already provide several digital solutions, for instance, our digital assistants, that make use of these technologies. AI and deep learning are certainly areas that I am curious to explore further. But when it comes to AI replacing human ingenuity, I would not expect that to happen anytime soon.
AI—and especially deep learning—are areas that I am curious to explore further. However, I do not expect AI to replace human ingenuity anytime soon.”
What interests you outside of the field of metals production?
Gurrath: I have two children, who are six and nine, and who keep my husband and I quite busy. I also play the clarinet in an orchestra. We concentrate on music written to commemorate important events such as the Hindenburg crash and on modern compositions such as the soundtrack from the TV show “Game of Thrones.”
One of the projects recently executed by Gurrath involved the modernization of the automation of a German steel producer’s second hot-rolling mill. The first mill had already been upgraded by Primetals Technologies in 2016, and it was Gurrath’s task to continue the partnership. Now that the project has successfully completed, the producer still receives updates whenever Gurrath implements a new feature or further refines the code. The collaboration also enables Gurrath to participate in the producer’s research efforts and to test out new features on real-world equipment.
Another project centered around a U.S. producer’s plate mill automation. Here, the challenge was that the aged equipment was providing only rudimentary production data—an issue that the producer wanted to address at a later stage. Despite this challenge, the team, including Gurrath, delivered the upgrade.