Eberhard Karnitsch-Einberger is head of Metallurgical Services at Primetals Technologies. Alongside degrees in Mechanical Engineering and Business Administration, he brings extensive global experience to his position, having held various leadership roles in Austria, Brazil, and Italy. From technical engineering and product management to executive positions, he has seen the steel industry from various perspectives and is always finding new ways to view the world. We asked him for his personal view on what if …
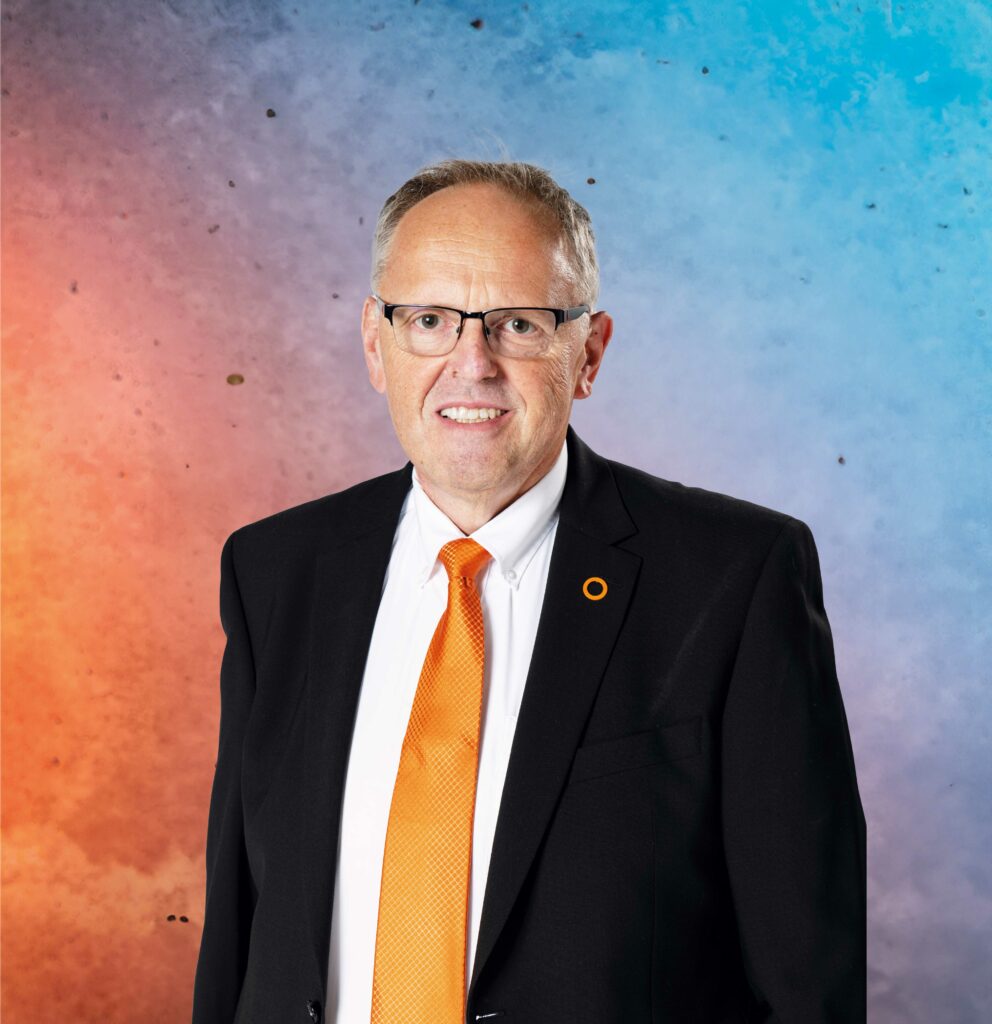
… we could define the human element in metal industry’s digital and sustainable transformation?
Eberhard Karnitsch-Einberger: In short, these are metallurgical services. At Primetals Technologies, metallurgical services integrate decarbonization and digitalization to reduce environmental impact, increase efficiency, and create new value for our customers. Rising cost pressure and a focus on sustainability require using every possible resource to streamline processes, including services. For example, Maintenance and Asset Technology (MAT), a fully digitalized asset management solution, is designed for the metals industry to give producers a complete overview of their equipment. Paired with our condition monitoring systems and m.space- our e.services platform of practical online tools, unexpected breakdowns are minimized. These digital solutions help reduce waste and increase efficiency for our customers and workshops. Moreover, our workshops embrace sustainable technologies, such as our location in Mexico, which now generates 98 percent of its energy from integrated solar panels. Our concept of services combines the human into efficient practices to improve maintenance activities that contribute to overall performance and safety.
… spare parts became a thing of the past as the lifecycle of mechanical aggregates increases?
Karnitsch-Einberger: Spare parts will never become a thing of the past for our industry. In the harsh operational conditions of a steel plant, aluminum, or copper rolling facility, especially where high temperatures are involved, it isn’t easy to imagine a world where parts would not eventually need replacing to ensure consistency, quality, and safety. What has been interesting is how spare parts may be handled in the future. Advancements in 3D scanning and heavy equipment manufacturing mean that tailor-made parts may be delivered by scanning the specific components that need repair or replacement. Following such scans, these types of parts could be replicated using additive manufacturing or 3D printing. Primetals Technologies could then ensure quality and safety standards with made-to-order spare parts as a spare part supplier. Additionally, innovative spare parts will combine condition monitoring systems with built-in sensors in the future to gain a proper understanding of operational conditions. Today, products, such as Extra Long-Life Bearings, come from past experiences working closely with maintenance teams at our customers and understanding operational conditions.
Metallurgical services integrate decarbonization and digitalization to reduce environmental impact, increase efficiency, and create new value for our customers.
… Primetals Technologies designed a caster that never required
maintenance?
Karnitsch-Einberger: The concept of a caster that never requires maintenance is more about shifting from repairs to precision maintenance. While the technology may not change drastically, maintenance practices will evolve with different maintenance technologies and condition monitoring systems. This will move towards predictive maintenance, where downtime is planned and often occurs based on a schedule. Therefore, plants will continue to require maintenance, but it will be less about sticking to scheduled downtime based on assumptions and instead executed with a higher level of certainty. These processes today are already more digital, scanning components and looking at datasets to track where, when, and how a specific component reached the end of its lifecycle. In the future, these components and spare parts will eventually “self-report” wear and tear. As mechanical components combine with smaller and more accurate sensors, digital tracking of spare and wear parts will become standard and automated. This type of plant would report its conditions to maintenance teams, facilitating scheduled maintenance and repairs.
… steel production fully integrated the use of artificial Intelligence and robotics?
Karnitsch-Einberger: When looking at the recent advancements in artificial intelligence (AI) and robotics, the development of the steel industry toward a fully automated plant with advanced robotics systems may not be a science fiction future. Recently, I have been intrigued by humanoid robots working in manufacturing environments, which redefines how we think about roles at a steel plant presently filled by employees, especially roles that involve potential risk to people. I also greatly appreciate the “robot dog.” It makes me think of a certain kind of future: we will have steel plants where employees monitor the entire operation of a steel plant as they would today but are supported by a team of humanoid robots and robot dogs. Capable of working in safer conditions while monitoring and operating the plant ensures increased safety. Meanwhile, the robots, backed by AI, could maneuver seamlessly throughout the steel plant and even operate in conditions that would be more dangerous for people at the plant. The application of robotics in today’s steel plants ensures that plants operate efficiently, as dangerous operations can be performed with more consistency and increased safety.
… various sectors worked together to overcome the challenges facing heavy industry?
Karnitsch-Einberger: Perhaps it sounds too trite, but “We’re all in the same boat.” I have experienced first-hand how the steel industry works in various countries. These approaches are diverse and often as multifaceted as the cultures and languages of the world. However, one unifying aspect has been finding opportunities for collaboration and communication. I see this occurring, although gradually, at scale across various sectors. With the global challenge of climate change and regulations regarding carbon emissions emerging worldwide, steel producers are reaching out to adjacent industries. Together, these industries are developing innovations and establishing a whole new economy with sustainability at the forefront. The steel industry’s challenges regarding emissions are strikingly similar to those of the energy, mining, or cement industries. Suppose we can build bridges and rethink and reconfigure our production processes. We can imagine processes that account for the reuse and recycling of waste materials, find opportunities for emissions reduction, and pathways for clean energy generation. I believe these significant hurdles can be overcome if proper connections are made.
Together, these industries are developing innovations and establishing a whole new economy …
… you could transform any aspect of the steel industry, what would you change?
Karnitsch-Einberger: If I could choose one aspect, it would be industry culture. I am a major proponent of “error culture.” Error culture differs from “error management,” which is often how our maintenance and service operations function, i.e., detecting and correcting errors to avoid future errors at all costs. Instead, error culture begins with people. What’s important is developing a culture that seeks to understand errors and improve based on these missteps. As a result, organizations would stand to gain much more than simply punishing or avoiding errors. Each could develop and improve from companies to heavy machinery through proper documentation, communication, and understanding of mistakes and errors. Of course, safety is the number one priority when speaking about heavy machinery, and errors should not be encouraged for the sake of progress if they involve risk to employees. However, engineers and development teams should thrive in a culture where they can push limits and test boundaries to discover growth opportunities.