A native of the Kazakh city of Aktobe, Andrey Kuzmin graduated with honors from the regional State University. After a career in the energy sector, he established himself within the construction industry in 2006 and headed a branch of a domestic company. He led the ARBZ project from its very beginning in 2012 until 2018. In 2014, he was the recipient of the “Altyn Sapa” accolade, which was awarded to ARBZ by the president of Kazakhstan in the category “Best Industrial Project.”
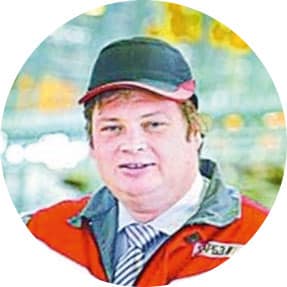
What prompted your company’s decision to invest in 2013, in spite of the worldwide recession in the steel industry that was still ongoing at the time?
Andrey Anatolyevich Kuzmin: There is a multi-year plan for the modernization of Kazakhstan, which requires investments to be planned based on a long-term vision. Within the framework of the “Industrialization Map” of Kazakhstan, the development of railway infrastructure is among the country’s top priorities. This has led to the decision to build the first plant in Kazakhstan for the production of rails. ARBZ is now among the most modern rail producers in Eurasia. It is one of only a few sites in the CIS region that manufacture premium rails using state-of-the-art technologies for rolling, thermal hardening, cambering, straightening, and inspecting. A fully automated platform integrates these technologies, guaranteeing the quality of the final product.
What were the key challenges that had to be met during the project?
Kuzmin: As the project had been initiated under the auspices of Kazakhstan Temir Zholy, the national railway company of Kazakhstan, there was significant pressure from all shareholders to complete the on-site construction work within the shortest-possible timeframe. Although tight, the project schedule was sound and rational, and all parties collaborated to meet the targets.
Was it possible to keep the project on schedule?
Kuzmin: Yes, a lot of work was done during the design, installation, and commissioning of the plant, which significantly sped up the plant’s startup. In the first year of operation, we were already producing about 140,000 tons of rails. I believe that there are no other cases anywhere in the world in which a plant was built from scratch in just 2.5 years, with rail production being mastered after only 6 months. In order to keep to this schedule, a great number of highly qualified specialists from several companies worked in unison.
Why did ARBZ choose Primetals Technologies as the main partner for this project?
Kuzmin: The original commitment from the stakeholders was very clear: to build a facility that would take a technological leadership role and would be capable of manufacturing top-quality products. Therefore, once the investment strategy had been outlined, ARBZ investigated which cutting-edge equipment and processes were available for rail manufacturing. The results from this investigation convinced us that the portfolio of Primetals Technologies had all the technologies, processes, and competences we required. Primetals Technologies was also chosen due to its reputation for being one of the most knowledgeable and reliable plant suppliers, with both technical proficiency and sound contract management. For example, Primetals Technologies’ inline-controlled hardening process “idRHa+” has proven to be very effective in obtaining high productivity levels in premium-rail manufacture.
How would you characterize the relationship with Primetals Technologies?
Kuzmin: A positive relationship was established between ARBZ and Primetals Technologies in the early phases of the project, and it remained this way over the course of the entire undertaking. Both parties showed eagerness to quickly resolve any problems, which greatly enhanced the teamwork. Of course, some situations with conflicting interests did occur, but they could be overcome thanks to the open-minded cooperation. Our mutual trust has always been solid, and the respective responsibilities were professionally met.
The mill is capable of manufacturing both rails and medium sections. What are the current percentages of these two product groups?
Kuzmin: Because of our long-term agreement with Kazakhstan Temir Zholy, rails represent the majority of our production. Aside from selling our products on the domestic market, our rails are currently exported to the Russian Federation and to CIS states. However, our equipment was designed for a quick changeover from the production of rails to that of structural sections, which gives us a great flexibility to adapt to different market conditions as they arise.
Could you comment on the state of the steel industry in the CIS region? What are its main challenges right now?
Kuzmin: In Kazakhstan and other CIS countries, the demand for steel products for both construction and engineering applications is set to moderately increase over the next few years. The main challenge is the imports from China and other countries. In order to remain competitive, it is crucial to constantly raise product quality, to conduct product research, and to focus on cost optimization. ARBZ will be continually improving the rail grades it can produce and will develop new ones, with the goal of enhancing rail performance, especially in terms of the rails’ resistance to wear and flaking. In order to increase our market share, we strive to foster excellent relations with our customers, as well as to widen our customer base. Geography is one of ARBZ’s biggest advantages: located right in the center of Asia, we are in the perfect position to serve Europe, Russia, the CIS region, and the Middle East.