This post is also available in: 简体中文 (Chinese (Simplified))
Each year, thousands of tons of perfectly good steel are scrapped at reversing cold-rolling mills. A new welding solution, referred to as the Cross Seam Welder (CSW), together with an innovative rolling technique, reduces scrap and can increase mill yield by more than 6%. The first orders for the CSW were received from JFE Steel Corporation in Japan.
Cold-rolling mills for the steel industry with production capacities of 600,000 t/a to 800,000 t/a typically employ a 2-stand reversing cold mill (2RCM) or two single-stand reversing cold mills (RCMs). Mills of this type continue rolling until the final pass with the leading and tail ends of the strip coiled on reels. Unrolled strip portions at both strip ends are scrapped. The quantity of scrap generated in a 2RCM typically accounts for about 6.5% of the overall production volume, and in a twin-stand RCM the scrap rate is around 2.5%.
To improve the overall strip-rolling yield in cold-reversing mills, engineers at Primetals Technologies have developed a new cold-rolling system in which continuous one-way rolling is performed. After each pass, the rolled coil is returned to the payoff position for the next pass until the prescribed strip thickness is obtained (Figure 1). This system can reduce the scrap amount to just 0.3%, which means a yield increase of more than 6% in a 2RCM. The main features of continuous one-way rolling are coil circulation, coil build-up, super-low-speed rolling and the new Cross Seam Welder (CSW) that is capable of joining strip up to 6.5 mm thick.
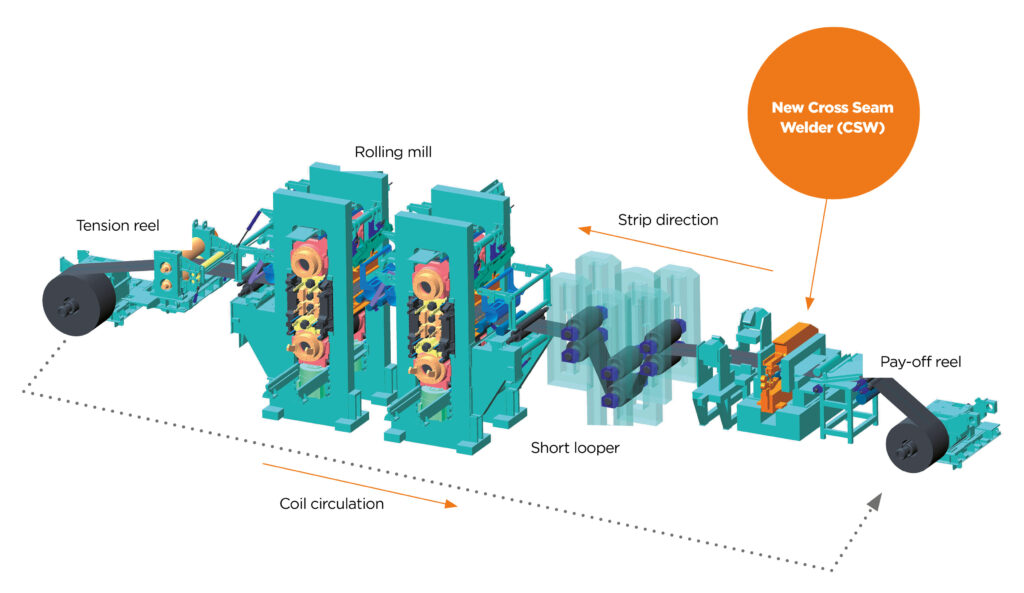
Cross Seam welder description
The CSW welder is similar to a conventional mash seam welder (MSW), namely that it also employs electric resistance welding. Figure 2 illustrates the CSW welding principle. With this welding method, the tail edge of the preceding coil and the leading edge of the following coil – both held by clamps – are simultaneously cut by a double-cut shear (not shown) and the cut ends are overlapped (View A of Figure 2). The lap is pressed and energized by the electrode wheel, and the heat generated by electrical resistance welds the lap together. The welder moves across the strip width and performs welding as it travels.
Compared to the CSW, the conventional mash seam welder has two principle weaknesses: one is a limited welding thickness of up to 4.5 mm, and the other is the step of the welded joint following welding. CSW has solved these problems by means of a so-called cross-swaging technique in addition to the application of a welding method that exerts a larger electrical current (Figures 3a and 3b). The latter softens the welded joint and makes it easier to deform the thicker part of the weld at high temperatures. Consequently, CSW is capable of welding strip with no step at all and is suitable for cold-rolling applications (Figures 4a to 4c). Thanks to the application of a larger electrical current, strip with thicknesses of up to approximately 6.5 mm can be welded (Figures 5a to 5c). Furthermore, because the CSW design is based to a large extent on the MSW, it additionally offers the benefits of low cost and compactness.
Fig. 4a: Macrostructure of cross section of as-welded strip
Fig. 4b: Results of 0-degree axial rotation of swaging rolls in relationship to each other immediately after the weld
Fig. 4c: Results of 3-degree axial rotation of swaging rolls in relationship to each other immediately after the weld
Fig. 5a: Macrostructure of cross section of as-welded strip
Fig. 5b: Macrostructure of strip cross section with cross-swaged weld
Fig. 5c: Welded and cross-swaged strip rolled to thickness of 1.0 mm
Other Csw application possibilities
In addition to its suitability for reversing cold-rolling mills, the CSW can also be used in pickling lines. Engineers at Primetals Technologies are further expanding the application possibilities of CSWs for welding applications in tandem cold-rolling mills. In conventional setups, the coils wound in the hot-rolling process are sent to the pickling line where scale is removed before cold rolling. The coils are joined by welders prior to the pickling process to enable continuous pickling. At many plants, flash butt welders are used and have often been in operation for decades. However, these welder systems are generally large and expensive, and are thus generally unsuitable for use in small and medium-sized mills. Another disadvantage is that a flash butt welder cannot weld high-tensile-strength steels (HSS) and other advanced steel grades – for which market demand is steadily increasing. Therefore, it is only a matter of time before flash butt welders will have to be replaced in existing pickling and cold-rolling lines. If ongoing tests at Primetals Technologies to weld HSS and special steel grades turn out to be successful, the new CSW may indeed prove to be a future-oriented welder alternative for steel producers.
CSW advantages and first industrial installation
The new Cross Seam Welder from Primetals Technologies offers producers the possibility to replace flash butt welders and laser beam welders used in pickling lines and tandem cold mills with substantial investment cost savings. In addition to its capability to weld thicker strip (up to 6.5 mm), the CSW also has the potential to weld a broad range of steel grades. In reversing cold-rolling mills, the combination of a newly developed continuous rolling process and the CSW will allow plant owners to profit from the thousands of tons of steel that don’t have to be scrapped.
The first order for the CSW was received from West Japan Works Kurashiki of JFE Steel Corporation, where it was installed in the No. 1 Continuous Pickling Line. Commercial operation commenced in April 2015. The second CSW order was from East Japan Works Chiba of JFE Steel where it will be used in the No. 5 Continuous Pickling Line following the scheduled start-up in April 2016.