Thomas (Tom) DeLuca joined Allegheny Ludlum (now ATI) in 1984 as a metallurgist after completing his university education in the field of metallurgical engineering at the University of Pittsburgh. He held a number of key management positions in the primary and finishing plants at various locations of Allegheny Ludlum. On September 1, 2012, DeLuca was appointed as Vice President and General Manager of Primary Operations for ATI’s Flat Rolled Products Group.
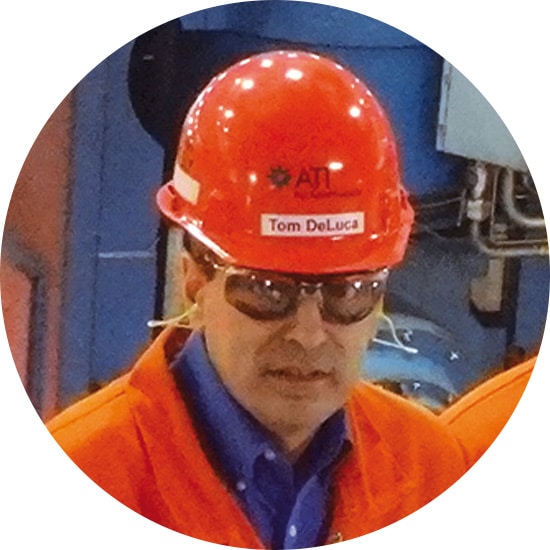
What were the main reasons for your company’s decision to invest in the HRPF?
Tom DeLuca: We saw the investment in the HRPF as an opportunity to replace two other 1950s vintage hot mills in our system. We also had the vision to lower our hot-rolling costs by using state-of-the-art automation. The facility has no slab yard, and has a totally automated coil yard. We also saw the opportunity to improve our finishing plant productivities and yields by maximizing the power and size card [capacity and efficiency] of the facility.
Why was Primetals Technologies selected as the main partner for this project?
Tom DeLuca: Primetals’ leadership in E&A [electric and automation], combined with tailor-made mechanical engineering, allowed ATI to develop what we believe is the most efficient and advanced rolling mill of its kind in the world. This, coupled with the single-source hardware supply, was an important consideration in our decision.
Primetals’ leadership in E&A, combined with tailor-made mechanical engineering, allowed ATI to develop what we believe is the most efficient and advanced rolling mill of its kind in the world.”
What were the key challenges that had to be overcome during the execution of the project?
Tom DeLuca: As with any large-scale project, there were a number of challenges in design, engineering, installation, commissioning and ramp up. Particularly during the latter stages of the project, we gained synergies from essentially integrating the Primetals commissioning engineers into our manufacturing team to jointly solve problems as they arose. In addition, unlike many other hot-mill installations in the world, ATI’s diverse product portfolio also represented a challenge that we were able to overcome in all phases of the project.
Did the supplied rolling mill meet your expectations in terms of operational reliability and flexibility?
Tom DeLuca: It did in several ways: Firstly, the flexibility of the combustion* and mill delivery system designed into this facility was unique to accommodate the broad range of products we manufacture. Secondly, qualification of the automation systems was performed relatively quickly. Furthermore, our collective teams shared a common goal to quickly ramp up mill production as well.
How is your company responding to ever-increasing environmental demands, especially with consideration to the Kyoto 2050 deadline that specifies a reduction of specific greenhouse gas emissions by 50% compared to 2005 levels?
Tom DeLuca: The HRPF is designed with state-of-the-art air and water quality systems that will easily be able to meet the strictest of environmental standards.
Has this investment enabled your company to enlarge its market presence or access new market segments?
Tom DeLuca: The mill’s designed power, size card capability and technology are unparalleled. ATI will be able to leverage this capability internally and externally for years to come.
*The combustion system includes the induction furnace, soaking pits, heat boxes for heat retention, and car-bottom heating systems.