Cold rolling of steel to produce tinplate places special demands on the rolling speed and thickness reduction. The high rolling speeds and thin gauges required, however, are often associated with problems related to unstable threading, poor strip shape and thermal scratching, all of which must be avoided or minimized. Primetals Technologies addresses these problems with an innovative continuous pickling line and tandem cold mill (PL-TCM), which is already in operation with impressive results at the steelworks of two Chinese customers.
To meet the surging demand for canning material in China, Primetals Technologies supplied an advanced continuous pickling line and tandem cold mill (PL-TCM) for tinplate applications to Shougang Jingtang United Iron & Steel Co., Ltd. (SGJT) and Wisco-Nippon Steel Tinplate Co., Ltd. (WINSteel) – Figure 1. The most advanced rolling technology is installed to enable faster and stable rolling of harder and thinner steel strip that fulfills the product demands for excellent shape, precise gauge control and thermal crown compensation. The 5-stand tandem cold mill features 6-high Universal Crown Control Mill (UCM-Mill) technology and the newly designed jet-pickling tank from Primetals Technologies. Steel is rolled to thicknesses down to 0.15 mm at rolling speeds of more than 1,800 m/min.
PL-TCM line layout
A general overview of the directly linked PL-TCM line configuration is depicted in Figure 2. Table 1 shows the main specifications of the line.
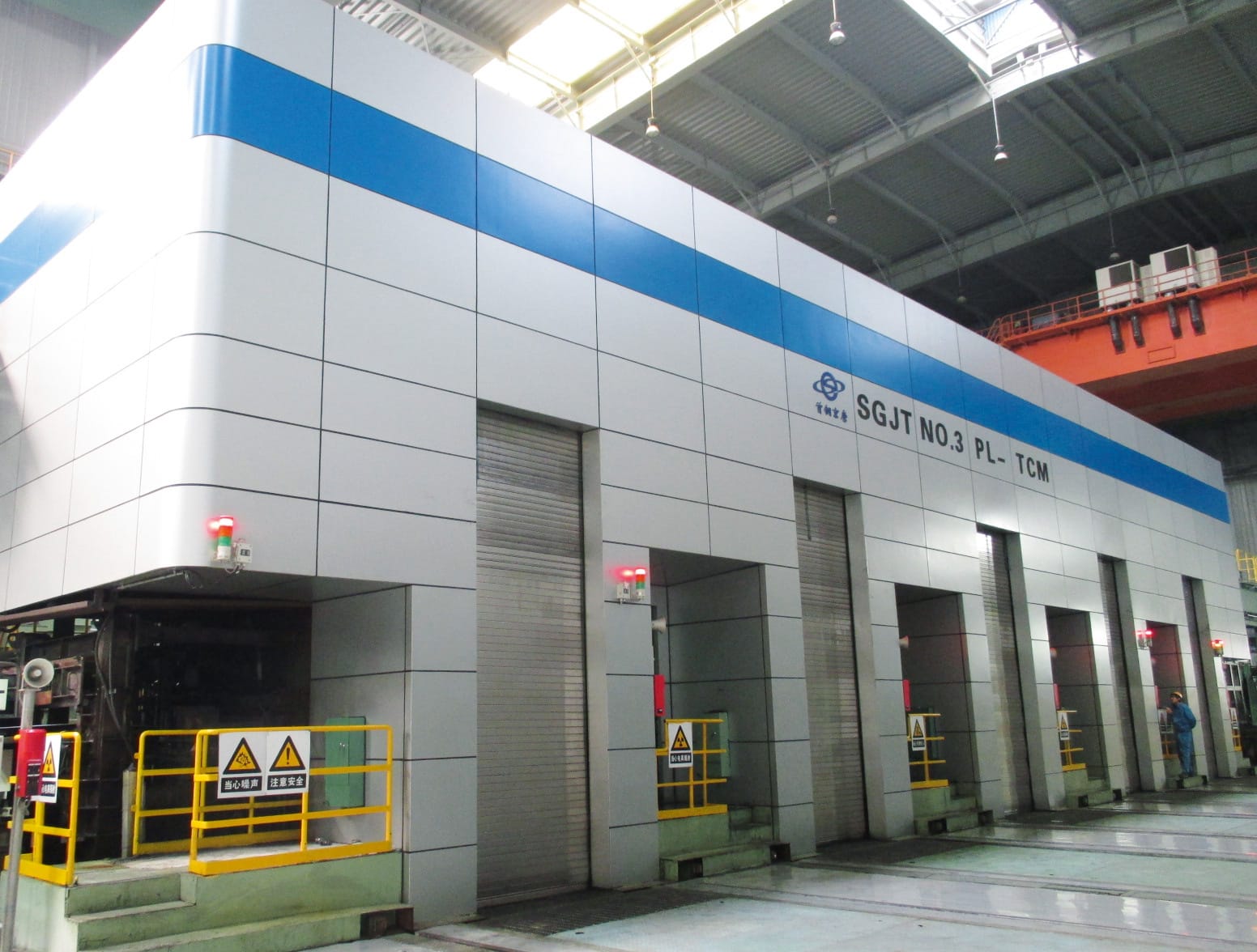
Entry and pickling section
A dual pay-off reel system is installed in the pickling line entry section to ensure uninterrupted pickling and rolling operations. With consideration to the thin strip gauges rolled in the cold-rolling mill, the coil-handling equipment, which includes coil opening and threading to the welder, supplies steel strip to the line in a reliable and controlled manner with a high degree of centering accuracy. Jet pickling is then performed at high speeds without over- or under-pickling. Following precise strip trimming, the strip is fed to the cold-rolling mill within specified speeds and also with high centering accuracy.
Tandem cold mill section
The 5-stand tandem cold mill (TCM) with 6-high UCM-Mill technology meets the requirements for harder, thinner, faster and more stable strip rolling. Steel is rolled to a minimum gauge of 0.15 mm at strip widths of up to 1,300 mm for the production of T2.5 to T5 tinplate. Maximum rolling speeds of more than 1,800 m/min have been achieved, making it one of the fastest rolling mills in the world. UCM-Mill technology, optimization of the mill guide arrangement and the configuration of the coolant system are decisive for preventing heat scratches on the strip surface – even at these high rolling speeds.
Required technologies to roll steel for tinplate applications
High-speed, heavy-reduction rolling with utmost gauge accuracy is required for the production of thin strip for tinplate applications at high productivity levels. Insufficient roll cooling can cause strip shape variations due to a growing thermal crown as well as potential heat scratching, which adversely affects strip surface quality and may also result in rolling-speed limitations. Furthermore, poor strip shape increases the frequency of strip breakage during strip width changes and may also result in unstable strip winding in the carrousel tension reel following shear cutting. Technical countermeasures for these issues are addressed in Figure 3.
Universal crown control mill
The UCM-Mill combines the advantages of excellent strip-shape-control performance and self-stabilization of the strip shape. Figure 4 shows the function principle of a UCM-Mill stand. The mill features axially shiftable intermediate rolls inserted between the work rolls and backup rolls. The intermediate rolls are shifted in conformity to the width of the strip to eliminate undesirable contact areas. Furthermore, this roll arrangement makes it possible to use smaller roll diameters and straight (without initial crown) work rolls for rolling all steel grades. The mill stand is also equipped with work-roll and intermediate roll-bending functions.
Mill guide system
Heat scratches caused by insufficient lubrication and cooling place limits on rolling capability with respect to rolling speed and strip-thickness reductions, yet high rolling speeds and heavy-gauge reductions are a prerequisite for steel produced for tinplate application. Thin-gauge rolling also increases the frequency of strip breakage. High-speed stable rolling with high-quality rolling results is achieved by optimizing the roll-coolant flow rate at each stand and for each strip-cooling zone. Oil-mist lubrication is also applied instead of grease-packed mill guide-roller bearings in order to reduce bearing friction. Accordingly, a secured and stable roll rotation during rolling-speed acceleration and deceleration with reduced strip tension prevents scratches between roll and strip surfaces. Liftable mill guide rolls are also installed to shorten handling time in case of strip breakage.
Thin-strip threading
Stable strip threading and winding into the carrousel tension reel (Figure 5) is required for continuous rolling. However, strip shape sometimes deteriorates during strip width changes when rolling thin strip. For strip thicknesses less than 0.2 mm, unstable threading and winding into the carrousel tension reel after strip cutting at the rotary shear often occurs due to strip buckling.
To correct this problem, a lower-friction threading-guide structure is installed as well as air blowing to reduce the friction between the guide and strip surface. These improvements result in stable strip threading and winding. Furthermore, an electrical magnet threading guide is applied to prevent buckling of the strip tail end after strip cutting and winding speed deceleration. This threading guide consists of four magnet sections. The magnets are independently energized to attract the strip upward, depending on the position of the strip tail end.
Successful start-up and commercial operation
The described PL-TCM facilities for the rolling of steel for downstream tinplate applications entered commercial production at SGJT and WINSteel in 2013 and 2014 respectively. The production of high-quality steel strip at thicknesses of only 0.15 mm and at rolling speeds exceeding 1,800 m/min was made possible with the use of UCM mill technology and by optimizing the mill guides and the coolant system.