thyssenkrupp Hohenlimburg’s medium-wide hot-strip mill in Hagen, Germany, received a digital assistant from Primetals Technologies for detecting strip cross cracks. The solution is a computer-vision-based system designed for this specific purpose.
thyssenkrupp Hohenlimburg, headquartered in Hagen, Germany, employs a staff of around 900. The plant produces strips for the cold rolling industry and direct processing, mainly for the automotive supply industry. Primetals Technologies has established a close partnership with the steel producer.
Computer-based Benefits
The computer-vision-based system quickly detects potential slabs carrying a cross-crack in the roughing mill. After entering the finishing mill, the cracks may spread, increase in size, and create holes in the rolled material. This defect can lead to cobbles in the finishing mill, with the risk of damaging the work rolls, backup rolls, and other production equipment. The primary benefit for thyssenkrupp is a reduction in downtime and wear related to the hot strip mill rolls.
The computer-vision-based system detects cracks early to prevent transfer bars carrying strip cross cracks from entering the finishing mill, allowing operators to take action before a crack leads to equipment damage.
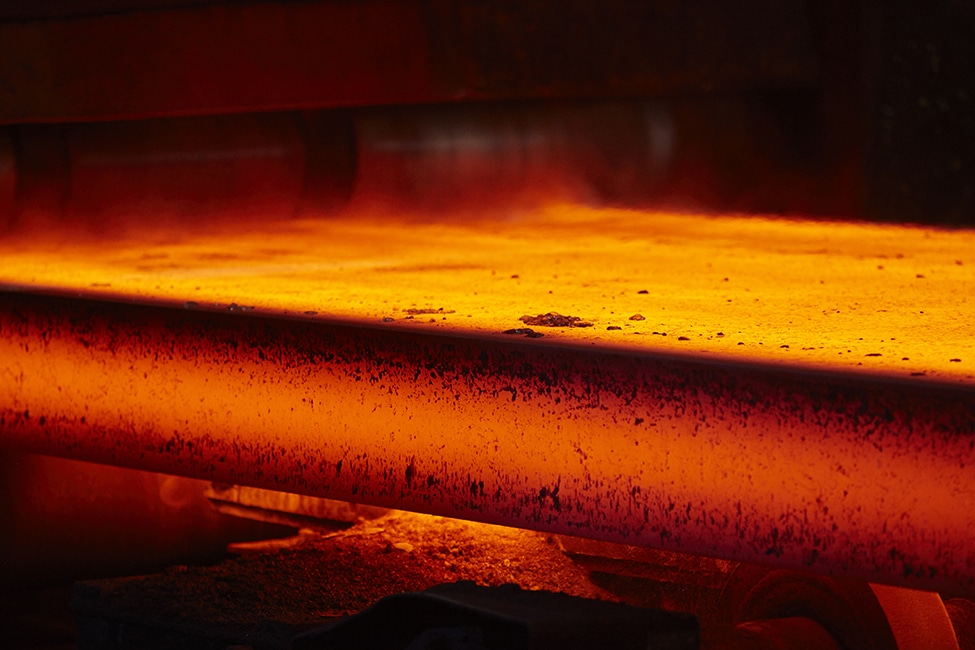
Rapid Alerts
The system utilizes a camera on the roughing mill’s exit side, and using a machine learning model, the assistant processes the stream and checks for cracks. When the assistant detects a crack, it quickly alerts the operators. Additionally, the information is transferred to thyssenkrupp Hohenlimburg’s intelligent business automation system for further analysis. The digital assistant will also continuously optimize its performance, as it is self-learning and can identify new types of cracks.
MORE INFORMATION
Click here to read the full press release, access contact details, and find other press resources.