He invented the world’s most innovative off-gas cleaning system, oversaw the development of numerous environmental solutions, became Head of Green Steel at Primetals Technologies, and was finally asked to shape the company’s future as Chief Technology Officer. In this interview, Dr. Alexander Fleischanderl shares his vision of what solutions will define the future of steel production in 2040 and beyond.
What will a best-in-class steel plant look like in 2040?
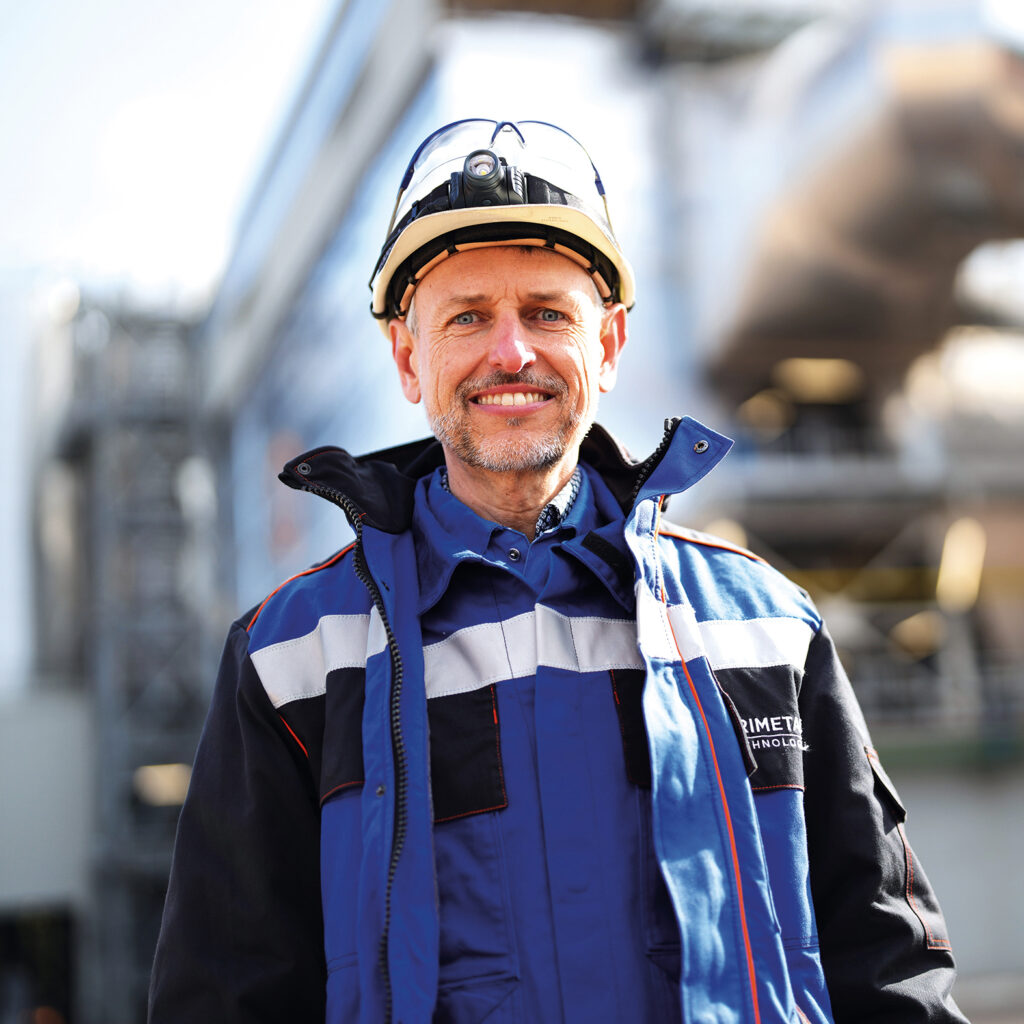
Dr. Alexander Fleischanderl: I believe that the answer to this question depends on what region we are looking at. Europe will likely experience the most dramatic changes in the coming decades. Any piece of production equipment that can be electrified will be electrified—enabling producers to leave fossil fuels behind. The circular economy will unfold more fully, thanks to solutions that facilitate advanced scrap processing, the reuse of slag for industries such as the cement industry, even more custom-tailored energy recovery systems, next-level drive systems, and many more. The ambition to reach “net-zero carbon” will extend into addressing Scope 2 emissions, which capture those indirect greenhouse gas emissions associated with energy purchases. Further advancements in automation will lead to greater efficiency and will make it easier to produce advanced high-strength and silicon steels. Moving closer to the autonomous plant—for instance, via our Central Operation Cockpit, which puts the entire production process at the fingertips of a single operator—will help resolve the challenging situation in the labor market.
Any piece of production equipment that can be electrified will be, enabling producers to leave fossil fuels behind.”
Are you happy with the progress the industry has made in becoming more sustainable?
Dr. Fleischanderl: Yes and no. On the plus side, there is more political will to bring about lasting change. The last four years have presented us with the European Green Deal, the U.S. Inflation Reduction Act, the Carbon Border Adjustment Mechanism, carbon taxes in many countries, and more publicly funded sustainability projects…
…and on the minus side?
Dr. Fleischanderl: The global use of fossil fuels is still on the rise. Reversing this trend will be especially challenging in developing regions such as India and Southeast Asia. At Primetals Technologies, we have defined a clear Green Steel strategy with KPIs to track the progress of our R&D initiatives and our accumulated order intake for all portfolio elements designed to make green happen.
Our efforts in innovation rest on two pillars: Green Steel and digitalization, which represent a ‘twin transition.’”
What measures are you taking to maintain the leadership role of Primetals Technologies in green steel production and beyond?
Dr. Fleischanderl: Our efforts in innovation rest on two pillars: Green Steel and digitalization. The two go hand-in-hand and are sometimes referred to as the ‘twin transition.’” We have defined our growth areas—e.g., direct reduction technology, electric iron- and steelmaking, advanced automation systems that include smart assistants, and next-level metallurgical services partnerships. Our global “Open Innovation” network includes universities, research centers, startups, and industry partners, all of whom are central to achieving this massive undertaking that is Green Steel.
Are you saying that Green Steel is too large a mission for any one company to tackle on its own?
Dr. Fleischanderl: Exactly, and it highlights just how important partnerships can be. At Primetals Technologies, we do have unique solutions that will define the future of ironmaking. One of them is HYFOR, a novel fine-ore reduction solution that requires no prior agglomeration and uses hydrogen as a reducing agent. Simultaneously, we are pioneering the HyREX technology in partnership with POSCO. This technology is also hydrogen-based and makes direct-reduced iron. In addition, we have a strong, long-standing collaboration with Midrex Technologies. Our parent company, Mitsubishi Heavy Industries, enables us to provide the world’s best carbon capture and storage solutions, with numerous references globally. Together, we can make an enormous difference on a global scale.
How far along is the industry in utilizing hydrogen?
Dr. Fleischanderl: We have entered a period of realism after going through a phase of slight overexcitement. However, hydrogen remains a crucial component of sustainable development. Once it becomes more widely available, it should primarily be used to directly replace fossil fuels. Hydrogen’s effectiveness in ironmaking is much greater than in areas such as transportation and mobility. These other fields can adopt hydrogen later once the groundwork and infrastructure have been established.
Will upstream processes become obsolete in Europe?
Dr. Fleischanderl: European energy prices will remain high for the foreseeable future, and the likely consequence is that we will experience a decoupling of the upstream and downstream processes. The upstream will largely be relocated to “upstream hubs” in regions like Australia, the Middle East, North America, and possibly North Africa, where energy and iron ore are abundant. Europe can then be a place of differentiation and focus on turning standard or intermediate products into high-end portfolio items.
As you would expect from the CTO of Primetals Technologies, Dr. Alexander Fleischanderl lives and breathes innovation. With more than 100 single patents registered under his name, he is a recipient of both the Siemens Innovator of the Year and the Mitsubishi Heavy Industries Best Innovation awards. His background in process engineering soon led him to the area of environmental solutions, where he pioneered technologies such as the renowned MEROS off-gas cleaning system. Before becoming CTO, Fleischanderl held the role of Head of Green Steel—a commitment that remains unchanged. While he is known to be a bit of a workaholic, Fleischanderl does have passions that complement his dedication to steel production. He greatly enjoys new digital technologies, self-made mediterranean cuisine, and long walks and hikes in the world’s remotest locations—where he finds time to reflect and to conceptualize innovations for the decades ahead.
Will the downstream area change as well?
Dr. Fleischanderl: All aspects of steel production will become more digital and sustainable. We are actively developing the green hot-strip mill, which runs solely on electrical energy. Silicon steel production is rising due to its use in electric cars, and our Hyper UCM is instrumental in producing these difficult grades.
Which of the world’s regions will shape the future of steel production the most?
Dr. Fleischanderl: As an Austrian, I am proud of the role my country has played in pioneering modern steel production with the LD converter—the BOF. I think that the combination of HYFOR and the Smelter has the potential to spark a similar revolution. I am also intrigued by recent Scandinavian greenfield projects such as BLASTR. Outside of Europe, the Middle East could become a rising region and start a new chapter in iron- and steelmaking at scale, driven by direct reduction.
With the invention of the LD converter, Austria pioneered modern steel production. I believe that the combination of HYFOR and the Smelter has the potential to spark a similar revolution.”
How are you responding to developing and transforming markets?
Dr. Fleischanderl: Let me single out two countries. India certainly has a great growth trajectory. Even though its reliance on the traditional integrated production route will continue, we are supporting Indian producers in moving toward greener methods today. For instance, we co-developed the Sequence Impulse Process (SIP) with thyssenkrupp AT.PRO, SIP increases the efficiency of blast furnace-based ironmaking and lowers the coke rate and the environmental footprint. We are in intensive discussions with multiple leading Indian steel producers with blast furnaces in operation. I also want to mention China, where we have started up 12 EAF Quantum furnaces to date. This highlights the country’s trend of moving toward electrification. This development will further strengthen with the availability of scrap increasing in the foreseeable. At Primetals Technologies, we have the solutions required for producers to fully embrace the all-electric route—from ironmaking to rolling, coiling, and strip processing.
Is Primetals Technologies devising new business models to meet the future needs of the steel producers?
Dr. Fleischanderl: Let’s use maintenance and services as an example here. New business models often correspond to the availability of new technologies, including digital solutions. Ultimately, service partnerships are about providing value to the producer in a way that compliments their strengths. We see a world in which every replaceable part in the plant has a QR code attached. It takes you to a manual and an easy-to-understand maintenance plan. We have developed an e-services feature called “m.buy” that provides maintenance staff with guidance on which spares to obtain and when to order them. As a result, prescriptive maintenance is already happening, rather than just predictive maintenance. We have contracts with some customers that compensate us based on the volume of steel produced. These arrangements reflect the degree to which we our interests are aligned with those of our customers—i.e., their success is our success.
Who are the current stakeholders investing in new large-scale, capital-intensive projects?
Dr. Fleischanderl: Even before I took on the CTO role, I made a point of engaging with very different members of the global metals community. This aspect of my work has now become absolutely essential. The recent shift toward sustainable steel has introduced new stakeholders who are genuinely driven by environmental concerns. Consequently, I am working with new partners in a variety of fields and disciplines: R&D collaborations, the energy sector, basic materials industries like the cement industry, the chemical industry, governmental and private funding, and many more. These new opportunities for cooperation are greatly inspiring, and I like the challenge of maintaining a holistic perspective.
Please complete the following sentence: “The biggest game changer in steel production in the coming decades will be…”
Dr. Fleischanderl: …new solutions designed to accelerate the electrification of steel production, as well as new direct-reduction technologies. I am especially excited about an industrial-scale prototype project of our HYFOR solution together with a Smelter in Austria. This project will, for the first time, realize a continuous production process with hydrogen-based reduction and represent an important step toward future-proof ironmaking in Europe and the world.