Head- and tail-end off-gauge length is defined as the length of strip from the weld to the point from which the final thickness deviation reliably stays within a tolerance band of approximately ±3%. Reprocessing costs of downgraded, off-gauge material can have a considerable impact on the final cost figure in rolling.
Moreover, high off-gauge lengths decrease the annual yield in quality product. To unlock this “hidden potential” of rolling-mill equipment, Primetals Technologies has developed a very cost-effective technology package called the Off-Gauge Optimizer (OGO).
Based on the perfect combination of technology, process control, and instrumentation, the OGO features a smart implementation of the control algorithms of a tandem cold mill based on the mass-flow principle.
The architecture of OGO is modular and consists of three parts: First, Advanced Mass Flow (AMFnew) controls the mass flow from the mill entry to the mill exit and ensures stable rolling conditions to keep thickness errors at a minimum. Second, Soft-Sensor for Strip Thickness (SST), a soft-sensor-based roll-gap-thickness estimator, perfects the performance of OGO during weld-seam-transition rolling. Interstand rollgap thicknesses are modeled based on strip speed data and one initial strip-thickness measurement. Third, Feed-Forward Control (FFCn-1) minimizes thickness errors that occur for reasons such as tension disturbances during weld-seam rolling on the next-to-last stand.
In the end, OGO significantly reduces the average off-gauge lengths—to approximately 8 m, as verified at several reference plants. For a plant with a production of 1.6 million tons per year, this corresponds to an annual increase in yield of approximately 6,400 tons.
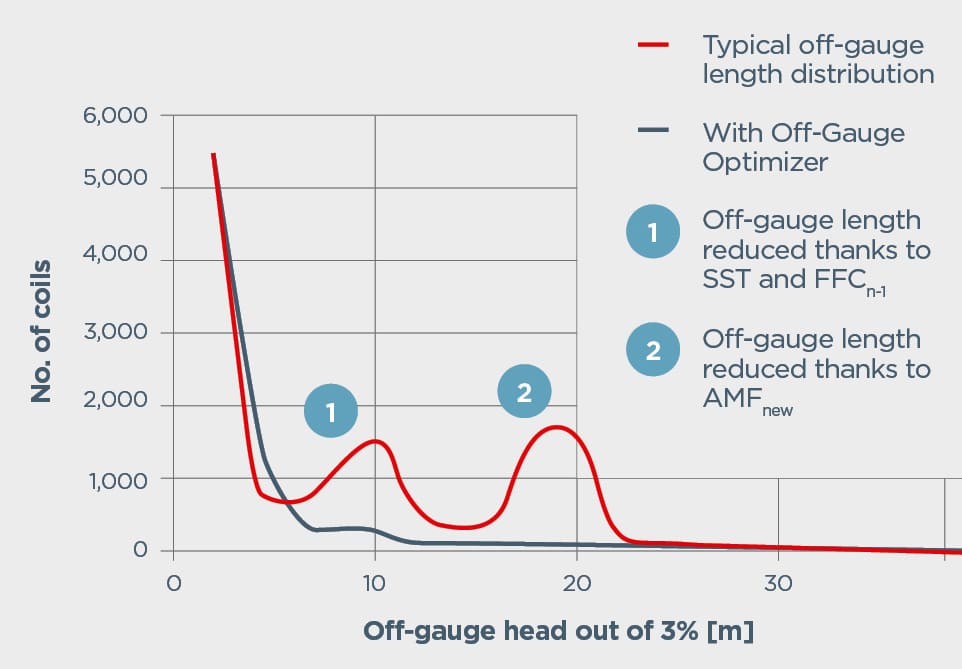