Salzgitter is investing in transforming its existing integrated steel plant into green steel production by 2033. The Salzgitter Low CO2 Steelmaking (SALCOS)* project involves two direct reduction plants and three electric arc furnaces to replace the existing blast furnaces and converters. Salzgitter has just signed a contract for the EAF Ultimate, an electric arc furnace with a tapping weight of 220 tons and an annual capacity of 1.9 million tons of steel to begin its transformation.
The SALCOS project will transform the steelmaking process from coal-based to hydrogen-based. Utilizing hydrogen, Salzgitter is expected to reduce CO2 emissions by 95%, or around 8 million tons. As a leading steel producer in Germany, Salzgitter has an annual capacity of 7 million tons of crude steel with 25,000 employees worldwide in 150 national and international subsidiaries and associated companies.
Green Steel Transformation
It underscores our ambition to remain a leader in the decarbonization of the steel industry and to set up the Salzgitter site for the future on a lasting basis. With Primetals Technologies, we have a strong partner on our side – true to our strategy of moving toward a sustainable industry”
Ulrich Grethe
Head of Steel Production at Salzgitter
With several recent EAF projects, low consumption figures, and competent project management, Salzgitter chose Primetals Technologies and the EAF Ultimate as the first step in their transformation. “Primetals Technologies is pleased to support Salzgitter AG’s decarbonization projects with the installation of a highly efficient EAF. With our Green Steel technology, we enable low CO2 steel production,” said Aashish Gupta, Executive Vice President and Head of Upstream at Primetals Technologies.
The EAF Ultimate
The EAF Ultimate is part of the electric steelmaking portfolio at Primetals Technologies, offering short tap-to-tap times, fully automated operation, and advanced control systems. The Salzgitter EAF features dust removal systems, a heat recovery system, a water management system, electrical compensation for grid stabilization, and material handling for alloying materials and additives.
The heat recovery system will convert much of the waste heat into steam which is then fed back and used in other production units. The tailormade Lomas off-gas analysis system determines all relevant values of the off-gas composition to ensure higher availability, reduced energy consumption, and increased safety measurements. It will also include Level 1 and 2 automation and the LiquiRob robot system for improved efficiency and safety. Part of the extensive digitalization package includes ALEX, a condition-monitoring system capable of identifying potential incidents before they occur.
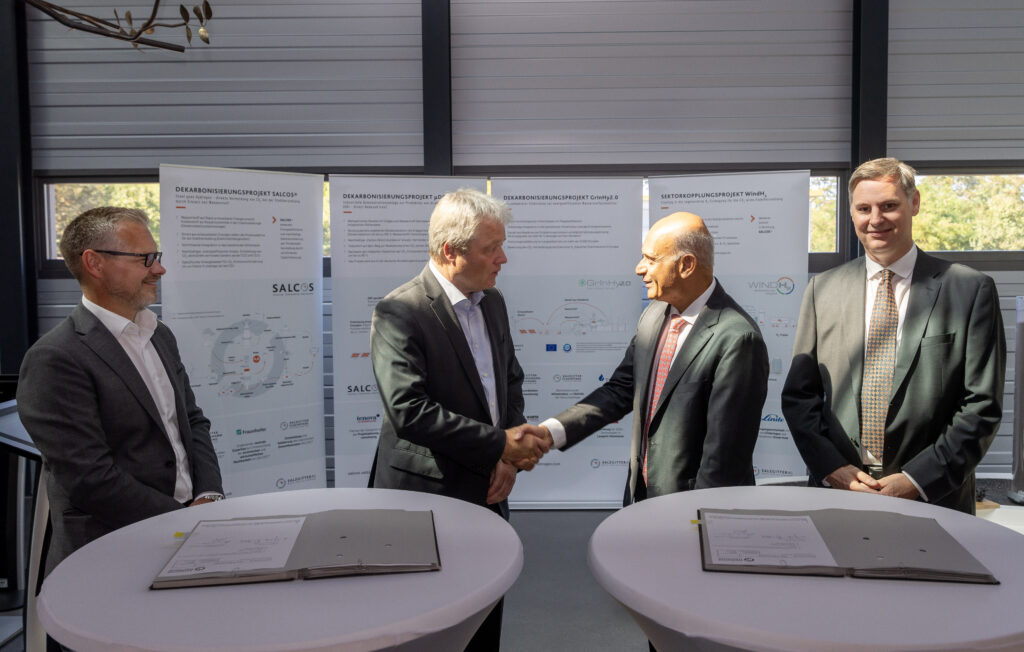
*SALCOS is a registered trademark of Salzgitter AG.
MORE INFORMATION
Click here to read the full press release, access contact details, and find other press resources.