In this session of Pioneers Talk, Bernd Linzer lets us in on the truth about Arvedi Endless Strip Production. A unique solution that combines thin-slab casting and rolling, Arvedi ESP is currently taking the market by storm, not least because of its green environmental footprint. But who is ESP for, and what steel grades can it produce? Tune in to discover the full truth about endless.
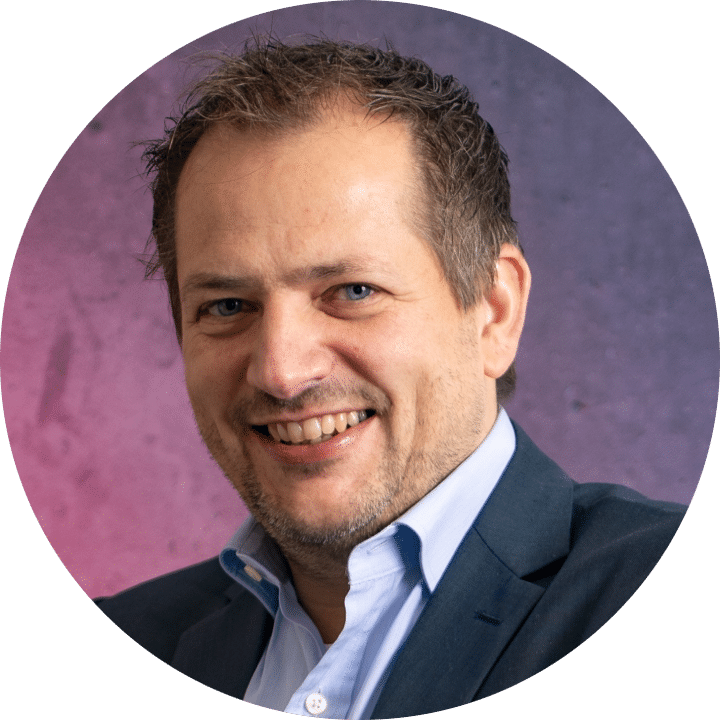
Interview with
Bernd Linzer
Hello and welcome to Pioneers Talk, my name is Tom Widter and today I have Bernd Linzer with me. Hi Bernd.
Linzer: Good morning, Tom, thank you for inviting me to this discussion.
You’re welcome. The reason why Bernd is with us today, is that Bernd is the Vice President of Endless Strip Production at Primetals Technologies, and he oversees both the technology and sales aspects of Arvedi ESP. Bernd, when we spoke about today’s session you mentioned something that I found rather interesting. I asked you what you really liked about your job, and you said it was finding the ideal plant configuration for every single customer and that it was very different from customer to customer. Would you be so kind to elaborate on how you find the ideal plant configuration?
Linzer: Right, you can imagine when you have different customers in different areas, so the markets are totally different and at the end of the day the customer wants to place his product on a certain market where it can range from very different products. It starts from thin strip to heavy gauges and for every customer the challenge is to find the optimum configuration and features to allow him to produce the best product on the lowest cost basis. This market involves many different products, starting from low carbon light gauges to pipe steel grates on very heavy gauges up to one inch.
Oh, wow that’s an extremely wide portfolio in terms of products. Is it possible to make all these grades with Arvedi ESP?
Linzer: Absolutely, we have different features we can implement into an ESP line that allows to produce all these steel grades and different steel products on these lines. We always try to give our customers the possibility to utilize the advantages of the endless production for all these steel grades. This is also linked to production costs and the quality of the strip. When it comes to the endless process you always have the possibility to reduce the very first meter of a strip until the very last meter of a strip with the same high-quality aspect, which would be impossible with a batch production.
So, it’s very consistent quality?
Linzer: Consistent quality, and you even have the opportunity to produce different strips in contrast to a conventional mill. Furthermore, you can even improve this by optimizing the alloying strategy for certain products to save costs.
Okay, so it’s a very efficient technology on many levels. I think one other argument that you can put forward is that the strip made with Arvedi ESP is the direct application of products. Does that mean that there is no, or hardly any other additional processing required?
Linzer: The big advantage of the endless production is that you can also target a very thin product which is ranging from 0.6 millimeters. This was recently done on a Chinese implementation on hot rolled strip, which is probably the world record. Hence, also ranging up with different steel grades in the very thin gauges like 1.5 millimeter for high strength material as well. This can be used to streamline the cold rolling process and to utilize this material, to go directly to the market. The advantage of the endless production is that you can range into the cold rolled thicknesses, which are well known on the market, but also within the product quality available with the cold rolling and with the ESP process. This can easily be made by adding a pickling or a pickling and galvanizing line downstream. The final product can be placed directly on the market instead of going through all the process chains of a fully integrated mill.
That’s interesting because that means if you combine an ESP line with an electric arc furnace you can make the whole plant radically more compact and probably much more efficient.
Linzer: Absolutely, and there are already certain implementations available and in operation on the market. For example, if you look to the carbon footprint of a fully integrated mill, starting from blast furnace, BOF, secondary methodology, then hot and cold rolling facilities followed by the downstream facilities. These steps can be replaced with a very compact implementation of an electric arc furnace, secondary methodology and an ESP line, which is able to produce the right products already in the thickness and mechanical properties capable to the market. Afterwards you only must add a pickling or picking and galvanizing line to come up with the same product as you have with the full integrated mill.
That sounds very intriguing, if I were a steel producer, on what kind of implementation time would I be looking at and at what kind of ramp up time would I be realistic?
Linzer: We can demonstrate that we have done this recently in very short times, hence with the changing market situation I would say the typical implementation time would be on global average something like 24 months. Hence, the ramp up time must be highlighted because this is where the customer starts to earn money. We can really be proud on some records we have done recently, where we have shortened the time as far as possible. We can guarantee that you can ramp up the mill to full production even including all the quality aspects for high value-added products.
Wow, I mean that sounds very confident, how many ESP lines have you implemented. It sounds like you have gained some experience, but how many have you done yet?
Linzer: Right now, we have 10 implementations where the 10th will be start up at the end of the year 2022, and the 11th will follow next year, so we have a very big experience in starting up these lines for sure. It is really the experience we have gained through different customers that enables us to build up a portfolio starting from thinnest gauges, lowest carbon contents within the steel grades, up to advanced high strength steel grades and everything available on the market.
Some of the countries you’ve sold ESP lines to have been Italy, China and the US. Is that correct?
Linzer: Yes.
With the trend towards electric steel making do you expect that demand will grow even further?
Linzer: Currently we have discussions all around the world, you can say that the carbon and the green steel topic is becoming more and more famous, and many companies are striving to optimize their carbon dioxide emission as far as possible.
ESP is already quite green, but can it become even greener in the future? That’s my last question by the way.
Linzer: Definitely, there’s always a possibility to optimize but we have done it already to quite an extent. If you compare a typical implementation of a fully integrated mill towards compact mills like an ESP line and an electric arc furnace, you can say that you can lower the carbon footprint of such a mill from of more than 2000-kilogram carbon dioxide per ton of steel down to a few hundreds. This is a dramatic reduction, and this is the only technology available where you can fully avoid these emissions within the ESP process and downstream.
As we can see, Bernd Linzer is pointing the way to the future, and I want to thank you for taking the time today to speak with us. We’ll be back with yet another episode of Pioneers Talk until then, goodbye thanks for watching.
Linzer: Thank you.
Pioneers Talk is the new video format of Primetals Technologies, focusing on informative and empowering interviews with experts in metals production and beyond. Topics extend to new advances in digitalization and automation, breakthroughs in green-production solutions, and success strategies for steel producers on all continents.
Bernd Linzer
Bernd Linzer is Vice President of Arvedi Endless Strip Production at Primetals Technologies, overseeing both the technology and sales aspects of the innovative endless casting and rolling solution. Bernd holds a ph.d with the University of Leoben, Austria, where he specialized in the field of thin-strip-casting technologies for carbon steels. When not further refining endless strip production, Bernd likes to ski, go for a deep-sea dive, or extend his knowledge of the world’s cultures by traveling.
Dr. Tom Widter
Tom Widter joined Primetals Technologies in 2016 and now works in the Marketing and Communications department. He is Editor-in-Chief of Metals Magazine, the company’s customer magazine, and co-host of “Pioneers Talk.” Tom cares deeply about didactics, style, branding, the future of metals, personal growth, and the Oxford comma.