This post is also available in: 简体中文 (Chinese (Simplified))
Dr. Takehiko Saito is one of the most distinguished inventors at Primetals Technologies. Over the last two decades, he has contributed to several dozen patent applications, chiefly in the area of cold rolling. He was part of the team responsible for the development of Cross Seam Welder technology, which is considered one of the major breakthrough welding solutions of recent years. We sat down with Dr. Saito to discuss his career, his innovations, and the nature of creativity.
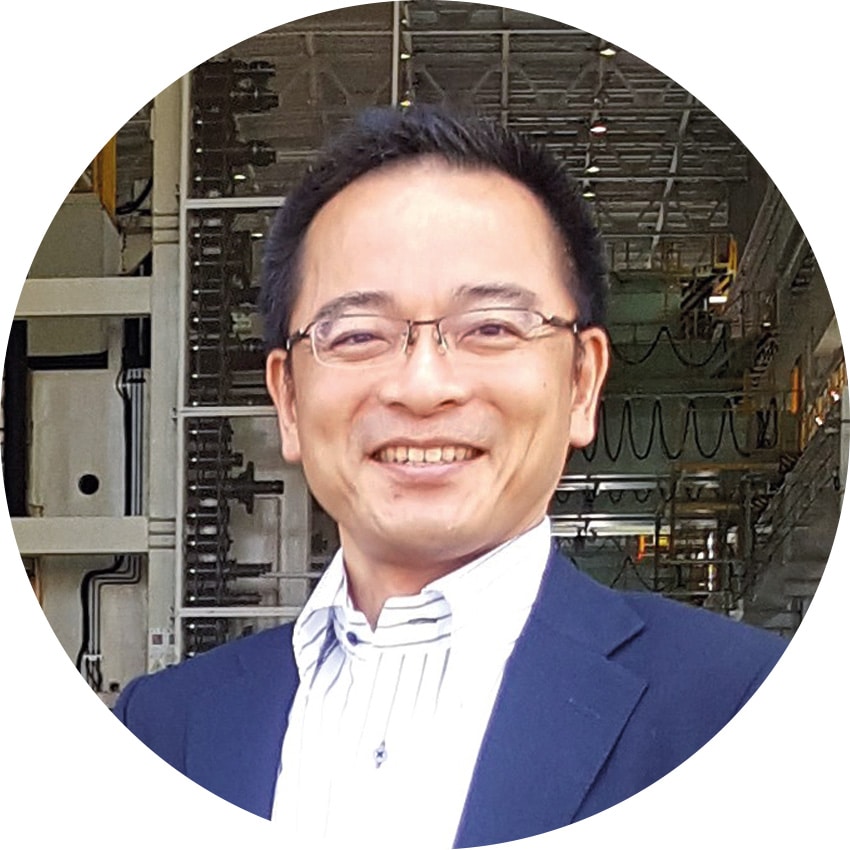
How many patents or innovations have you been involved with during your career with Primetals Technologies and its predecessor companies?
Dr. Takehiko Saito: I have tried to count the patents that I have been involved with during my time at the predecessor companies of Primetals Technologies, namely Hitachi and Mitsubishi-Hitachi Metals Machinery. The number I got was a total of 44 patent applications over 20 years, of which 30 patents have been registered up until today. These patents are, of course, the achievement of not just myself, but the teams that worked on the various projects. In the case of one of my senior colleagues from the Technology & Innovation Department, the total I get is 80 patents in 35 years. And Dr. Hirai, the CTO of Primetals Technologies, has been involved with the patents for more than 130 items. So I think that I really should aim to engage in even more patents and innovations in the future.
What, in your opinion, was the most economically successful innovation for the company?
Saito: First, I should say that the technology I have been involved in has had a long history of innovation related to steelmaking machinery. While I have made certain contributions, there have been numerous areas that I was not directly engaged in. Having said that, I think that one of the most successful innovations is the Universal Crown Control Mill (UCM-Mill), including the High Crown Control Mill (HC-Mill), both of which I was not previously involved in, but today am so profoundly associated with. When I was looking for a job some 23 years ago, I visited Hitachi’s Mechanical Research Laboratory and brought with me presentation materials from my academic background. I was aspiring to land a research position related to the rolling-machine business of Hitachi, because I was highly impressed with the innovations of the UCM-Mill and the HC-Mill. It was a true turning point in my life. I feel that there is a mission to continue to supply the brand and the know-how that make up the UCM-Mill to the world, just as we inherited it from our predecessors, because the UCM-Mill is still the flagship technology of the cold-rolling mill.
Which innovation are you most proud of personally?
Saito: This would be the Hyper UCM-Mill and the Cross Seam Welder (CSW). These two products actually won the Technology Development Award from the Japan Society for Technology of Plasticity in 2011 and 2014. The Hyper UCM-Mill has dramatically improved the rolling performance of the standard UCM-Mill. It has the advantage of achieving a higher productivity while lowering the customer’s capital expenditure. The CSW has substantially advanced the welding performance associated with more conventional mash seam welding machines. It allows for wider product specifications and has a larger market due to its very competitive price. I am particularly proud of the appreciation that the CSW has received. About a decade ago, a freshly founded team, consisting of Noriaki Tomi- naga, Shinichi Kaga, Mitsuru Onose and myself, conceived a new approach. It was called “Compact Continuous Cold-Rolling System,” and the Cross Seam Welder was one of the central innovative components of the larger concept. There has, of course, been further research and refinement of the process around the CSW since its first inception. As of today, we have sold this technology twice and are expecting additional orders to come in soon.
Are most of your ideas and innovations the product of a persistent systematic approach, or do they generally occur as the result of chance or coincidence?
Saito: I think that ideas and innovations come together when there is a fusion of both a wide range of general knowledge and deep expert knowledge. This is necessary when someone tries to solve technical issues either continuously or intermittently. The question then becomes: how much time does it take to solve a problem? In Japan, we have a saying that it takes the right “seeds” for certain “needs” to change into “wants.” If we apply this to the Cross Seam Welder, then its seeds were born during the first development steps of the Compact Continuous Cold-Rolling System. We then improved these seeds to fit the needs of our customers, and in doing so, we changed their needs into wants. Overall, this process took a decade, and I believe that having a continuous ten-year-long development process is important, particularly when the research process has different phases of varying intensity.
In your view, is creativity something that a person is born with, or is it something that can be fostered with proper training and education?
Saito: I would have to say “yes” to the second part of the question, as I believe that education plays a major role. The fusion of curiosity, creativity, basic knowledge and expertise leads to inspiration and concrete solutions. Dr. Clayton Christensen, a professor at Harvard Business School, lists in his work five essential skills that innovators have to have: associating, observing, questioning, experimenting and networking. Christensen suggests that it is possible to increase one’s abilities through active learning. Also, I think that it is an essential ability for creative people not to fear failure, but to seek new challenges instead. To remind myself of this, I wrote down a quote from film director James Cameron in my notebook. It reads, “Failure is an option, but fear is not.” In my opinion, this is a fantastic motto for innovators.
In many parts of the world, it is often just a single person or small group of people working together who generate innovative ideas – for example, Steve Jobs and Steve Wozniak, who assembled their first computers in a garage. Is it like this in Japan, or you do feel that Japanese ideas and innovations tend to be more consensus-driven and the result of a collective effort?
Saito: Again, I would turn to Dr. Christensen’s research to answer this question. In his work, he differentiates between two types of innovation, namely sustaining and disruptive innovation. Sustaining innovation is a business model in which the supplier provides continuously improved products to existing customers. If I apply the model of needs, seeds and wants again in this context, one could say that sustaining innovation requires the supplier to always strive to satisfy the needs of his higher-end customers. A collective consensus is then important, because it is necessary to satisfy the needs of existing customers by bringing together experience and knowledge. Disruptive innovation is a business model that sees the supplier providing a very affordable product that yields a high profit for new customers. So this would mean that these customers’ needs would have to be transformed into wants by the supplier’s seeds. One such disruptive innovation has been the minimill. This type of innovation is best attempted by small groups of people, as in your example of Apple, because there is an aspect that should not be judged by the existing sense of values. What I have taken away from Dr. Christensen’s work is that innovation is not so much country-specific as it is dependent on the type of innovation that one wants to achieve.
I wrote down a quote from film director James Cameron in my notebook. It reads, ‘Failure is an option, but fear is not.’ This is a fantastic motto for innovators in my opinion.”
Do you think that there are any aspects to Japanese innovation culture that are unique in the world?
Saito: I don’t think so, and even if there was such a distinction, I would much rather attribute it to the idea of “diver- sity within a single world.” However, I do think that “cool Japanese culture” is a unique trend in popular culture, and an innovative one at that.
Is there any singular inventor or scientist from the past that you particularly admire or who was been an inspiration to you?
Saito: To be honest, there is no one inventor who inspires me more than others. However, when I was a child, I was very aware of Thomas Edison’s invention of the incandescent light bulb. This was because from 1880 to 1894, bamboo from my hometown of Yawata City was used for the filaments. It was said that these bulbs reached lifetimes of 1,000 hours and more.
What innovations or technical solutions are you working on right now that stand out from the rest?
Saito: I am trying to transform the Compact Continuous Cold-Rolling System into a disruptive innovation within the cold-rolling area. I cannot go into more detail here, but this development will come soon, once the needs change into wants on account of our new seeds.
Researcher and innovator
Takehiko Saito was born in Fukushima Prefecture and raised in Yawata City, a comparably small town located in Kyoto Prefecture. Having acquired a Master’s Degree in Mechanical Engineering at the Kyoto Institute of Technology, Saito started work at Hitachi, a predecessor company of Primetals Technologies, in 1994. Nine years later, Saito’s department within Hitachi became part of Mitsubishi-Hitachi Metals Machinery (MHMM), where Saito investigated thickness and shape control methods in the ultra-low speed range, strip breakage initiated by a step around the welded part, and many other issues within the field of cold rolling. Importantly, Cross Seam Welder technology also originated at MHMM. Having become a specialist in the area of plastic deformation of metal and an expert in the rolling theory of cold rolling, Saito earned a Ph.D. from Nagoya University in 2014 for his studies on the application of a mash seam welder to continuous cold rolling. In 2015, both MHMM and Saito became parts of Primetals Technologies. Besides “all things cold rolling,” Saito is passionate about recent developments in the area of virtual reality technology, which he would like to see become an integral part of the control pulpit of steel plants in the future.